The Basic Principles Of Alcast Company
The Basic Principles Of Alcast Company
Blog Article
Not known Incorrect Statements About Alcast Company
Table of ContentsAn Unbiased View of Alcast CompanyHow Alcast Company can Save You Time, Stress, and Money.The Ultimate Guide To Alcast CompanyGet This Report on Alcast CompanyFascination About Alcast CompanyThe Best Strategy To Use For Alcast Company
Chemical Comparison of Cast Aluminum Alloys Silicon advertises castability by lowering the alloy's melting temperature level and boosting fluidness throughout casting. Furthermore, silicon contributes to the alloy's strength and wear resistance, making it valuable in applications where resilience is essential, such as automobile parts and engine components.It likewise improves the machinability of the alloy, making it simpler to process right into ended up items. By doing this, iron adds to the total workability of aluminum alloys. Copper increases electric conductivity, making it useful in electrical applications. It also enhances deterioration resistance and includes to the alloy's overall strength.
Manganese adds to the stamina of light weight aluminum alloys and enhances workability (Aluminum Casting). It is generally utilized in wrought light weight aluminum products like sheets, extrusions, and accounts. The existence of manganese help in the alloy's formability and resistance to splitting during manufacture processes. Magnesium is a light-weight aspect that provides stamina and influence resistance to aluminum alloys.
Little Known Questions About Alcast Company.
Zinc improves the castability of light weight aluminum alloys and helps regulate the solidification process during casting. It boosts the alloy's toughness and solidity.

The primary thermal conductivity, tensile strength, yield stamina, and prolongation vary. Select ideal basic materials according to the performance of the target product produced. Among the above alloys, A356 has the highest thermal conductivity, and A380 and ADC12 have the least expensive. The tensile restriction is the contrary. A360 has the most effective return toughness and the highest prolongation rate.
Getting My Alcast Company To Work
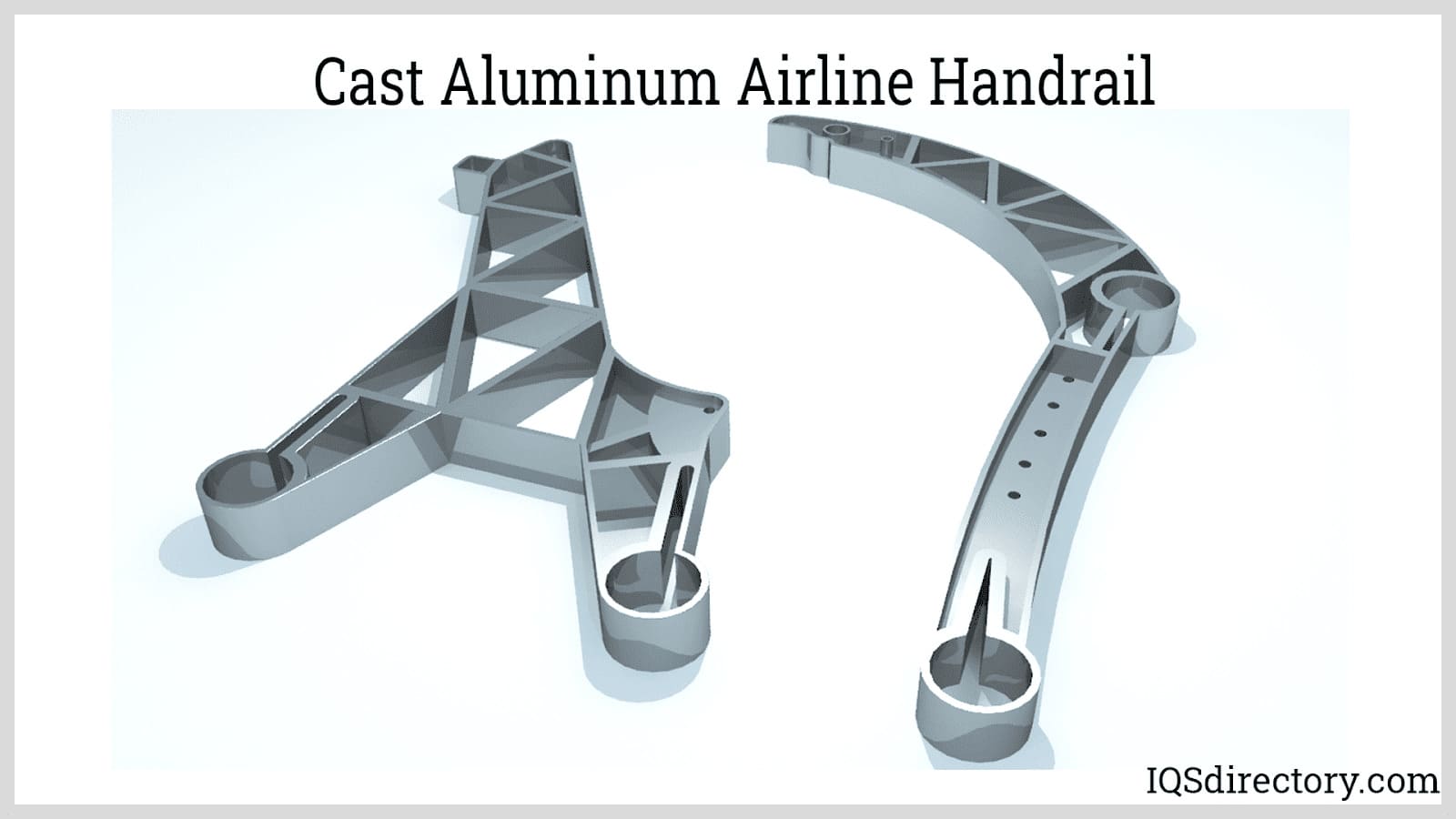
In accuracy spreading, helpful hints 6063 is appropriate for applications where intricate geometries and top quality surface area coatings are paramount. Instances include telecommunication enclosures, where the alloy's remarkable formability permits smooth and cosmetically pleasing designs while preserving architectural honesty. Likewise, in the Illumination Solutions sector, precision-cast 6063 elements develop elegant and effective illumination components that need complex shapes and good thermal performance.
The A360 displays premium prolongation, making it suitable for complicated and thin-walled parts. In precision spreading applications, A360 is appropriate for sectors such as Customer Electronics, Telecommunication, and Power Tools.
The Single Strategy To Use For Alcast Company
Its special homes make A360 a valuable selection for accuracy casting in these industries, enhancing item toughness and high quality. Light weight aluminum alloy 380, or A380, is a widely used casting alloy with a number of unique features. It uses superb castability, making it an optimal choice for precision casting. A380 shows excellent fluidness when molten, guaranteeing detailed and in-depth molds are accurately reproduced.
In accuracy casting, aluminum 413 beams in the Consumer Electronic Devices and Power Equipment industries. This alloy's superior deterioration resistance makes it an outstanding selection for exterior applications, making sure resilient, long lasting items in the pointed out markets.
9 Simple Techniques For Alcast Company
The light weight aluminum alloy you select will considerably affect both the spreading procedure and the properties of the final item. Due to the fact that of this, you need to make your choice meticulously and take an informed method.
Figuring out the most ideal light weight aluminum alloy for your application will suggest considering a broad variety of characteristics. These relative alloy attributes adhere to the North American Die Casting Organization's guidelines, and we have actually divided them into 2 categories. The initial category addresses alloy qualities that affect the manufacturing process. The second covers characteristics impacting the homes of the last item.
Our Alcast Company Statements
The alloy you select for die spreading straight affects numerous facets of the casting process, like just how easy the alloy is to function with and if it is prone to casting issues. Warm fracturing, likewise recognized as solidification fracturing, is a common die casting flaw for aluminum alloys that can cause interior or surface-level rips or fractures.
Certain aluminum alloys are a lot more vulnerable to hot cracking than others, and your selection needs to consider this. It can damage both the cast and the die, so you ought to look for alloys with high anti-soldering properties.
Corrosion resistance, which is already a notable feature of aluminum, can vary significantly from alloy to alloy and is an important characteristic to consider depending on the environmental problems your item will be exposed to (aluminum foundry). Use resistance is one more residential property generally sought in aluminum products and can differentiate some alloys
Report this page